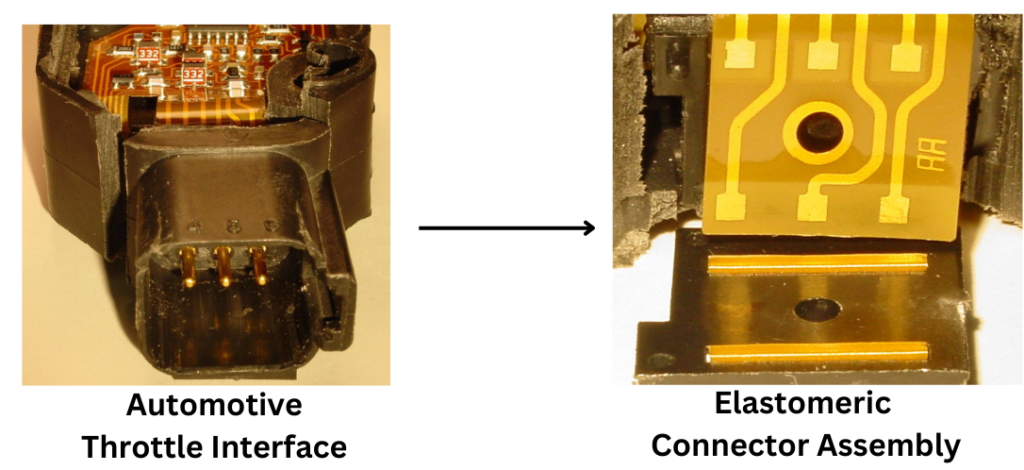
The demand for reliable, cost-effective, and scalable electronic solutions is higher than ever, especially in automotive assemblies. A recent project involving Z-Axis Connector Company’s elastomeric connectors showcases their potential to streamline automotive module integration. This case study explores how these connectors provided a robust solution for mating flex-circuits to external wiring harnesses in an automotive application.
Challenge
An automotive supplier required a dependable connection between a multi-row flex-circuit and external wiring harnesses in one of their modules. The primary challenge was to achieve high reliability and precise alignment while minimizing manufacturing costs and tolerances. The flex-circuit needed to accommodate six unique contact pads, demanding a versatile and cost-effective connector solution.
Solution
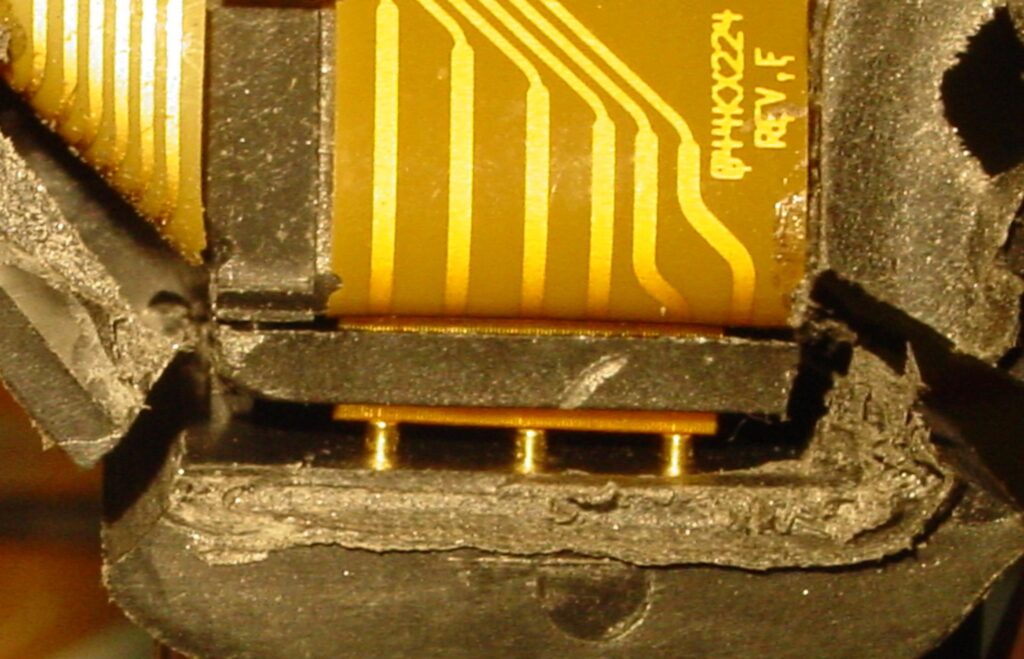
Z-Axis Connector Company introduced their elastomeric connector elements as the ideal solution. Two key components were used:
- Elastomeric Connector Elements: These elements provided a compliant interface between the flex-circuit and contact pins. Their ability to span across the flex-circuit contact pads ensured reliable electrical connections.
- Holder for Elastomeric Elements: A custom holder was designed to retain the elastomeric elements securely in position, ensuring consistent contact alignment and stability.
Implementation
The integration process involved:
- Accurate Alignment: The flex-circuit and contact pins were precisely designed to ensure accurate alignment, which was crucial for maintaining reliable connections.
- Cost-Effective Manufacturing: The compliant nature of the elastomeric elements allowed for relaxed manufacturing tolerances. This significantly reduced production costs without compromising on performance.
- Multi-Row Flex-Circuit: The solution efficiently handled the six unique contact pads of the multi-row flex-circuit, ensuring robust electrical connectivity across all connections.
Results
The adoption of Z-Axis Connector Company’s elastomeric connectors led to several notable benefits:
- Reduced Costs: The use of compliant elastomeric elements minimized the need for stringent manufacturing tolerances, leading to lower production costs.
- Reliable Performance: The elastomeric connectors provided consistent and reliable electrical connections, crucial for the automotive module’s functionality.
- Simplified Assembly: The custom holder facilitated easy assembly and secure positioning of the elastomeric elements, enhancing the overall manufacturing process.
Conclusion
Z-Axis Connector Company’s elastomeric connectors proved to be a game-changer for this automotive application. By addressing the challenges of cost and alignment, these connectors enabled the supplier to deliver a high-quality, cost-effective solution. This case study underscores the versatility and reliability of elastomeric connectors in demanding automotive environments, making them a preferred choice for modern automotive applications.